A Guide on how to use Conical Slicing
This is a quick run-down on how to use the transformation scripts developed by the ZHAW in Winterthur, Switzerland to perform conical slicing yourself.
I forked their code on GitHub to make it easier usable and fixed some bugs. For the moment, I’d recommend working with the scripts found here:
https://github.com/RotBotSlicer/Transform/tree/master/Scripts%20for%20Variable%20Angle
Pre-Requisites
PYTHON
The scripts used to require an installation of Python on your machine. If you’re familiar with Python, you can skip this part. If you never used Python a simple way is to install and use the ANACONDA Python distribution that you can download here:
https://www.anaconda.com/products/distribution
Install it and run the SPYDER IDE.
ANACONDA comes with all required libraries for the scripts, only Numpy Stl is missing.
https://anaconda.org/conda-forge/numpy-stl
To install it within ANACONDA copy and past the following command into your Python console within SPYDER IDE:
conda install -c conda-forge numpy-stl
SLICER
You can basically use any slicer for conical slicing and Simplify3D still works the best, yet to make this method easier and accessible, everything you see here has been done with SuperSlicer:
https://github.com/supermerill/SuperSlicer
Most slicers won’t allow slicing parts in negative space so you will have to move the origin of your slicing profiles coordinate system to the center of the bed.

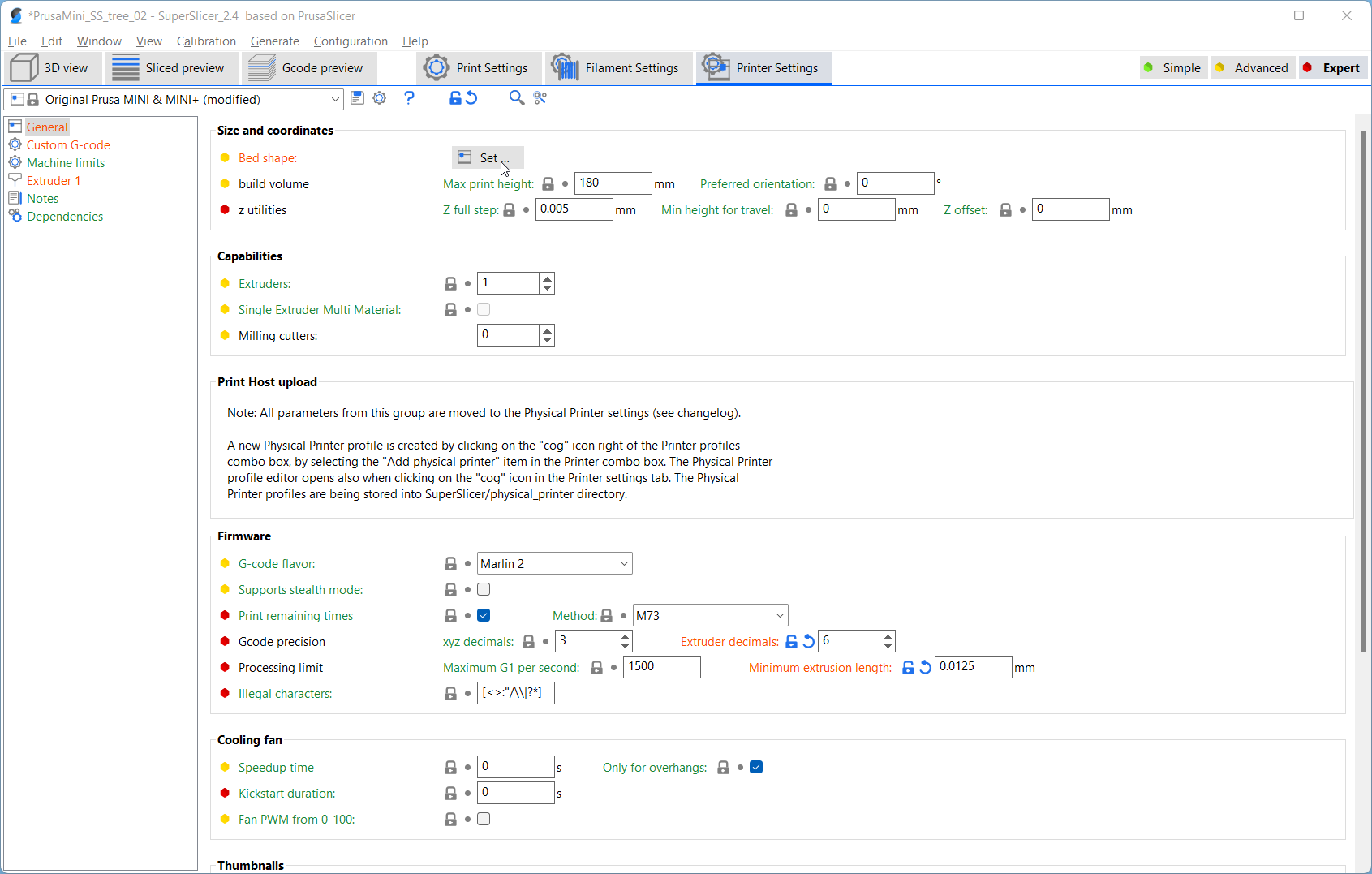
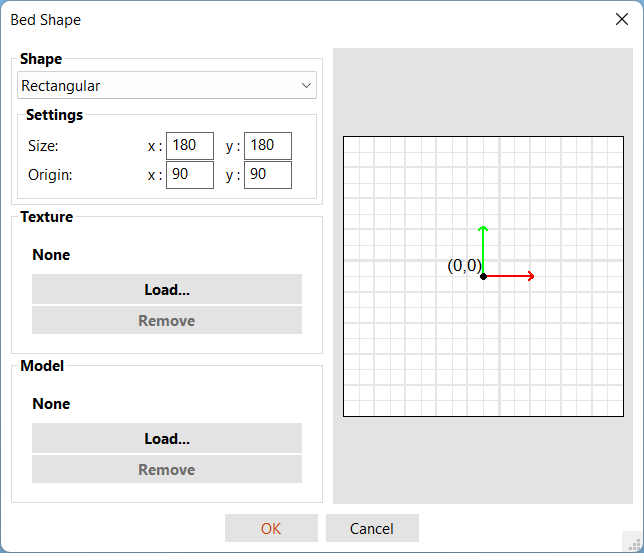
STL preparation
Any STL can be used for the method, yet if you prepare your files in CAD I recommend adding a manual brim for better bed adhesion.
Part with brim
In order to properly transform the part, the STL mesh needs to be relatively fine. The transformation script allows for crude refinement of the mesh, yet if you are able to export a refined mesh from CAD the final results will be even nicer.
Refined mesh in Fusion360 with 0.5 mm maximum edge length
Import your stl into the slicer. The z-axis of the slicing coordinate system will later be our conical axis. Move the part so that the cone axis is where you want it.
Positioned part
Now we need to use a stupid workaround because PrusaSlicer has an unfixed bug and will always calculate it’s own model origin, regardless if “Auto-centering” is switched on or not. If you don’t do this script, the conical axis will be inconsistent messing up your results.
Place a dummy box, as big as your print plate into your project and make sure it’s perfectly centered, filling the whole build area.


Now you export the whole project as stl, which saves the defined positioning. Save the file in an stl subfolder relative to where you saved the Python scripts.
Export Plate as STL
Transformation
Open the Transformation_STL_var_angle.py script in SPYDER IDE (or your Python IDE of choice). Make sure there is a stl_transformed subfolder existing. At the top of the script enter the filename of the stl you just exported, set the cone angle and set a reasonable amount of refinement iterations. 0 or 1 works with regular fine meshes, for many parts 2 or 3 is what you want to go for. Also, set the type of cone you want to use for the transformation. Run the file and wait for it to finish.
Slicing
Now go back into your slicer and load the transformed file from the stl_transformed subfolder. If everything worked well, it should be transformed and positioned so that the slicing axis and the cone axis of your part are at the same location. The pain geometry and the positioning dummy are now one part that need to be separated again. The dummy can then be deleted.

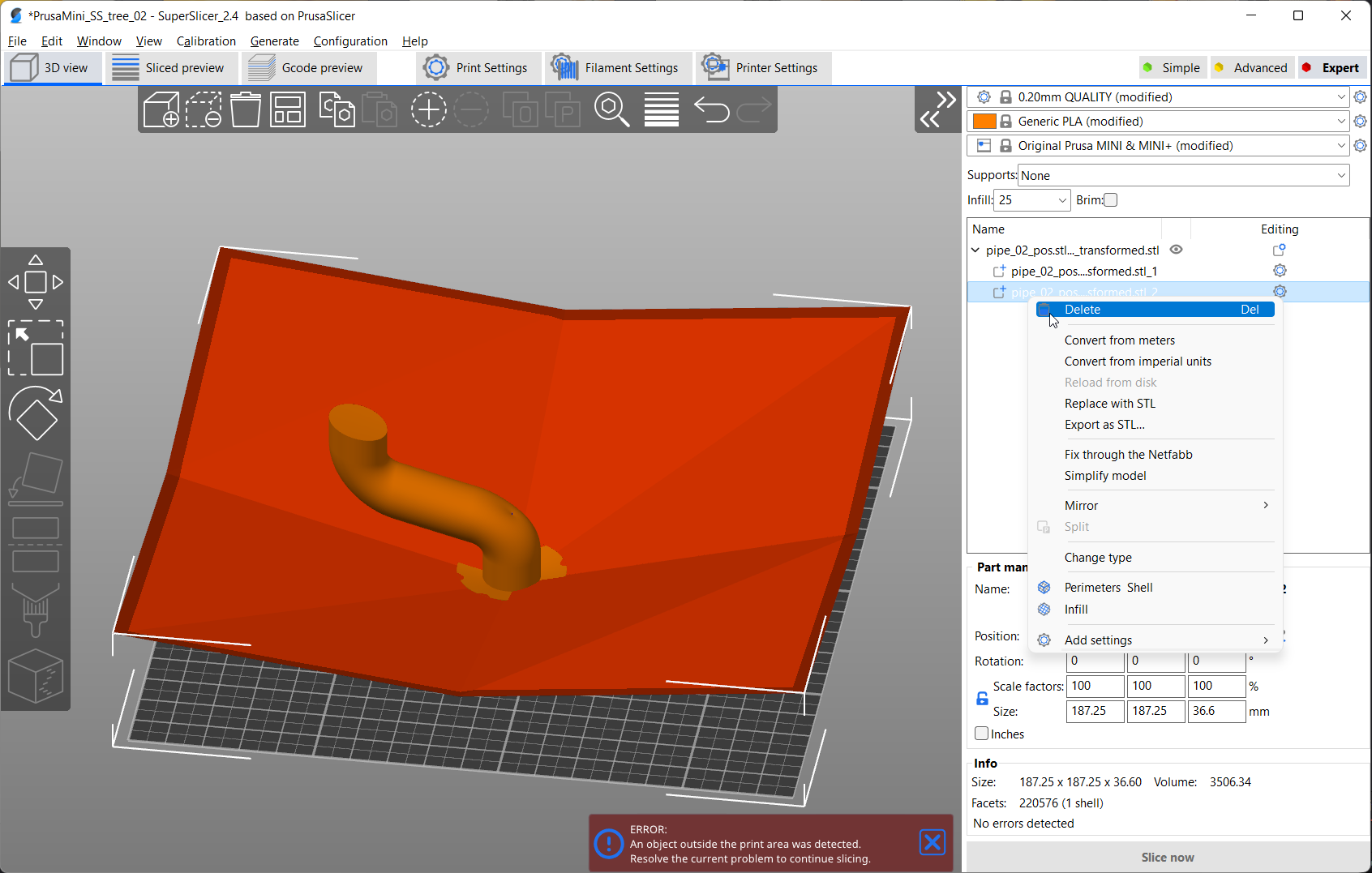
You can now slice the part, just as any other one. My parameter set is certainly not perfect but it’s the best I came up with so far:
0.25 mm layer height
3 Perimeters
2 Top Layers, 0 Bottom Layers
25% Cubic infill
No Skirt, no brim
Relatively low printing speeds to allow for enough cooling time: 15 mm/s on perimeters, 25 mm/s for infill
0.45 mm extrusion width
Flow to 90 - 95%
Disable fan for the first 5 - 10 layers
All G1 commands within the G-Code will later be transformed and with this also your prime lines and everything that’s in the start G-Code which can mess up the back transformation. My script will ignore G0 commands during the back-transformation, so if you want to keep your prime line, change the G1 commands to G0. Most printer firmwares will handle them the same way anyways.
You can find a sample profile here, that you can easily adjust for your personal machine:
https://www.printables.com/model/314844-supportless-christmas-tree-conical-slicing



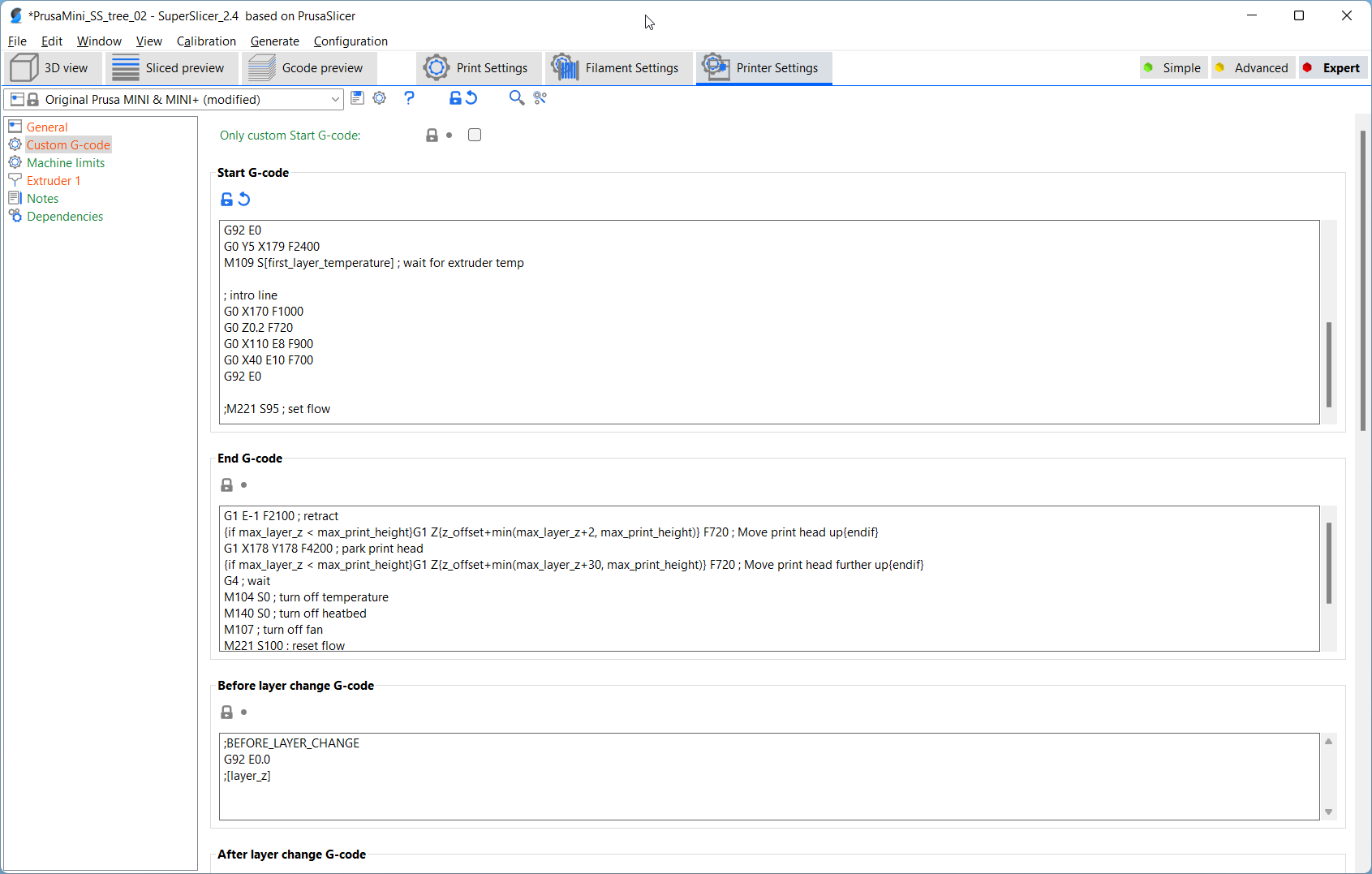



Safe the G-Code into the gcodes subfolder.
Sliced part
Back-Transformation
Open Backtransformation_GCode_var_angle.py in SPYDER IDE. Insert the name of your G-Code file you just exported and make sure you set the same slicing angle as when transforming the stl and run the code.
This will backtransform the G-Code and create the Conical Printing commands. You can check the results of the transformation using a G-Code Viewer like the one that comes with PrusaSlicer and SuperSlicer.
Conical G-Code