Bondtech CHT High Flow Nozzle Reviewed
Regular 3D printing nozzles look all pretty much the same on the inside. There is one drilled hole that’s slightly bigger than your filament diameter that goes almost all the way to the tip at which point the small orifice bore starts that defines your nozzle diameter. There is some slight variation with the cheapest ones just drilled with a standard 118° drill tip. E3D tried to improve on that many years ago with a stepped bore probably to improve internal flow but now uses as many other higher-quality manufacturers a special drill bit with a pointier tip for better flow characteristics. Ultimaker still uses a special stepped geometry in their AA-print cores maybe for less oozing during retracts. Though these are all just slight variations of a simple design.
This right here is Bondtechs new CHT nozzle that features a special core that splits up your filament into three separate channels. CHT means Core Heating Technology which means that the material is not only melted from the outside in, but also from the inside out promising higher melt rates. Bondtech is actually not the one who came up with this idea. Maybe you have already seen the Matchless nozzles from 3DSolex that have been around for a while, though never been particularly popular. Bondtech has now licensed the core heating technology and made their own version of it. They licensed it because it’s unfortunately patented by 3DSolex but I’ll get to that later.
Bondtech CHT
The CHT nozzles are a drop-in replacement for your standard E3D and RepRap nozzles with an M6 thread though you can even use them on an Ender-3 and its derivatives. There is an Ender-3/MK8 version in the making so watch out for this one because the current version is 0.5 mm shorter and will therefore require re-leveling. It’s a high-flow nozzle and therefore currently only comes in sizes starting from 0.6mm up to 1.8mm, though I would like to see a 0.4mm variant as well. The Bondtech CHT is made from brass with a nickel coating that protects against corrosion and makes the surface less sticky to plastic but is not as wear-resistant as hardened steel for example and is therefore not suitable for your carbon fiber materials. I was happy to see that it’s at least, in my opinion, very reasonably priced at 20 bucks so won’t break the bank. Before we cut one open and try to figure out how looks on the inside and gets manufactured let’s see how it performs and benchmark it against a standard V6 nozzle and I think ways more interestingly an E3D Volcano!
Bondtech CHT, V6 & Volcano Nozzle
For our first performance test, I’ve compared the 0.6 mm variants. To make the tests as comparable as possible, I’ve done them all on the same E3D Hemera using the same heater cartridge, thermistor, and for both standard V6 as well as the Volcano used silicone socks for insulation.
The extrusion test is really simple and I basically just tell the extruder to feed 200 mm of filament and weigh the extruded spiral of material. I then gradually increase the extrusion speed.
M104 S240 ; Set Nozzle Temperature G1 X60 Y20 Z60 F10000 ; Go to extrusion position M83 ; Relative Extrusions G4 G1 F200 ; Prime G1 E20 G4 P2000 ; Wait 2 seconds G1 F125 ; Set Extrusion Speed in mm/min HERE G1 E50 ; Extrude 50 mm G1 E50 ; Extrude 50 mm G1 E50 ; Extrude 50 mm G1 E50 ; Extrude 50 mm G4 S0 G1 E-5 F1000 ; Retract 5 mm
At some point, the hotend won’t be able to properly melt the material anymore which results in more back-pressure and more and more slip in the extruder gears. At that point less material gets extruded, which I can measure with my scale. Just to give you an idea of what normal and high melt rates are take a look at these examples. With normal prints using a standard 0.4 mm nozzle at 0.15 mm layers we’re mostly printing at around 5 mm³/s or less. Using a 0.6 mm nozzle with thicker 0.35 mm layer we max out at around 15 mm³/s because this is often the limit of normal extrusion systems so profiles are tuned for that. If you want to effectively use even bigger nozzles or go faster, high flow extrusion systems are necessary.
So let’s get to the test. I first benchmarked the reference, a 0.6 mm V6 nozzle. As just said, with this standard setup we can usually go up to 15 mm³/s extrusion rate which I again confirmed by this test. At that point, we already under extrude by 5%, anything more and the extruder will start severely stripping and skipping. At 20 mm³/s the results are unusable anymore with 25% of under extrusion. Let’s compare that to the standard high-flow setup from E3D, the volcano, which significantly increases the length of the meltzone. Using this setup we can basically double the extrusion rate and under extrude around 5% at 30 mm³/s after which point things get really bad and unusable. Let’s now change back to a standard length heater block and install the Bondtech CHT nozzle. 15 and even 20 mm³/s didn’t seem to be a problem and we still get perfect flow. At 30 mm³/s, which was the limit for the volcano setup, we can see the curve is slightly getting worse but we’re still only under extruding by 2%. At 40 mm³/s we’re just reaching the 5% under extrusion limit and are this way 33% better than the Volcano and almost 200% better than our standard V6 nozzle which is unbelievable. If we go even higher we can clearly see that we reached the limit of the CHT, but man, better performance than a volcano hotend at the size of a V6 nozzle.
The thing that was interesting to observe was the change of melt behavior. At slow speeds, flow is nice and even. At faster rates, the melt swell seems to become quite significant probably from all the internal stresses and at some point we even see really interesting melt inconsistencies which also shows that we’ve reached the limit of the setup. Another thing I noticed was that the volcano hotend seems to ooze more material than the short nozzles, probably because there is a higher volume of material that get’s heated and expands which might have a negative impact on stringing and print quality. Talking of higher melt volume or a longer meltzone – a reason why the Volcano might fall short of the CHT even though it has a longer meltzone is, that exactly this longer meltzone causes additional fluid drag therefore limiting flow.



I also did the same test with a 1 mm nozzle which restricts the flow less and allows the volcano to be usable up to 45 mm³/s though the CHT 1 mm performed like a champ up to 60 mm³/s and only started skipping at 90 mm³/s which is probably more than you will ever need!
Okay, so where do we continue now? Well, to better understand how the nozzle is manufactured and how it looks on the inside, I, of course had to sacrifice a brand new one and cut it open on my CNC router. This nicely shows the yellowish brass base material with the nickel coating on the outside and we can get an idea of how they probably manufacture the unique geometry.
Sectional cut of a CHT nozzle (0.8 mm)
Instead of one straight bore they drill 3 times at an angle which all terminate at the same point. The sharp edge of the divider, I think, was done when they pilot-drilled with a bigger bit. I assume they first pilot drill with a bigger bit to create the sharp edge and then use a 1.2 mm bits for the material channels.
Suspected manufacturing steps
Really clever design and I bet tricky to manufacture at this size if you’re not careful. The thing that surprised me at first but gets clearer if we take a look at my reverse engineered CAD model, is that the core, for which the C in CHT stands is way smaller than one might expect and looks more like a blade that splits the filament rather than significantly contributing to the heating of the material.
Reverse-engineered cross section of a CHT nozzle
As cruel as might be to some, but I actually drilled out the divider on one nozzle and tested it. The results showed that it still performed way better than a standard nozzle but has a significantly worse performance at higher melt rates compared to the unmodified one and even slightly falls short of the volcano.
Extrusion performance without the heating core
So the filament splitter significantly contributes to the performance but the other maybe even more important and smart design of the CHT is the increase of the heating surface by the cloverleaf shape that the 3 bores generate. A single circle is just the physically worst choice for heating something because it has the smallest circumference compared to the area. Any deviation from that is better, though a circular hole is obviously the easiest to manufacture. Secondly, since plastics are such a bad conductor of heat the distance from where you heat to the center of the material is also crucial, which is smaller with the cloverleaf shape compared to a circle.
Comparison of different shapes for material channels
Having the heating core in at least part of the nozzle makes that even better and due to the sharp edges, it also shouldn’t constrain the flow too much. And then there is the overall conical shape of the material channel which I can’t fully judge but might also lower flow resistance and gradually decrease the distance from the hot walls to the center of the material. Overall a top-notch design, which also shows in the more than impressive melting performance. But how does the design with the melt splitter and the undercut at the heatbreak do in a realistic printing scenario where you have retractions and travel moves?
Heating simulation of different shapes with similar area (besides the last one)
The retraction and stringing test printed with the 0.6mm nozzle looked very comparable and even with this high amount of retracts there didn’t seem to be any clogging due to the CHT shape. Bigger nozzles have the tendency to string more and the amount I’m seeing seems reasonable. My own Mini-Me and a 200% scaled-up Marvin looked almost indistinguishable with even a bit better overhangs using the Bondtech nozzle. The other prints that I did with the 0.6 and 1.4 mm CHT nozzle turned out really well. My 200% Mini-Mi took an hour to print with extrusion rates up to 40 mm³/s. The print looks great just the amount of cooling that the Prusa provides is the bottleneck at some point and the layer doesn’t properly solidify before the next one is printed on top. I first had failures at higher extrusion rates on the 300% Benchy due to thermal runaway but adding a silicone sock fixed that. Just by doing the maths, the 40W of the heater is plenty to melt that amount of material. There were some areas with a bit of underextrusion at 40mm³/s but I’m certain that 30 or even 35mm³/s would have worked well with Prusas extrusion system. Cold pulling a CHT nozzle for cleaning purposes is possible, yet I only managed to do it once, though I carefully burnt out one nozzle successfully, but don’t recommend it because I’m not sure if that might chip the nickel coating.


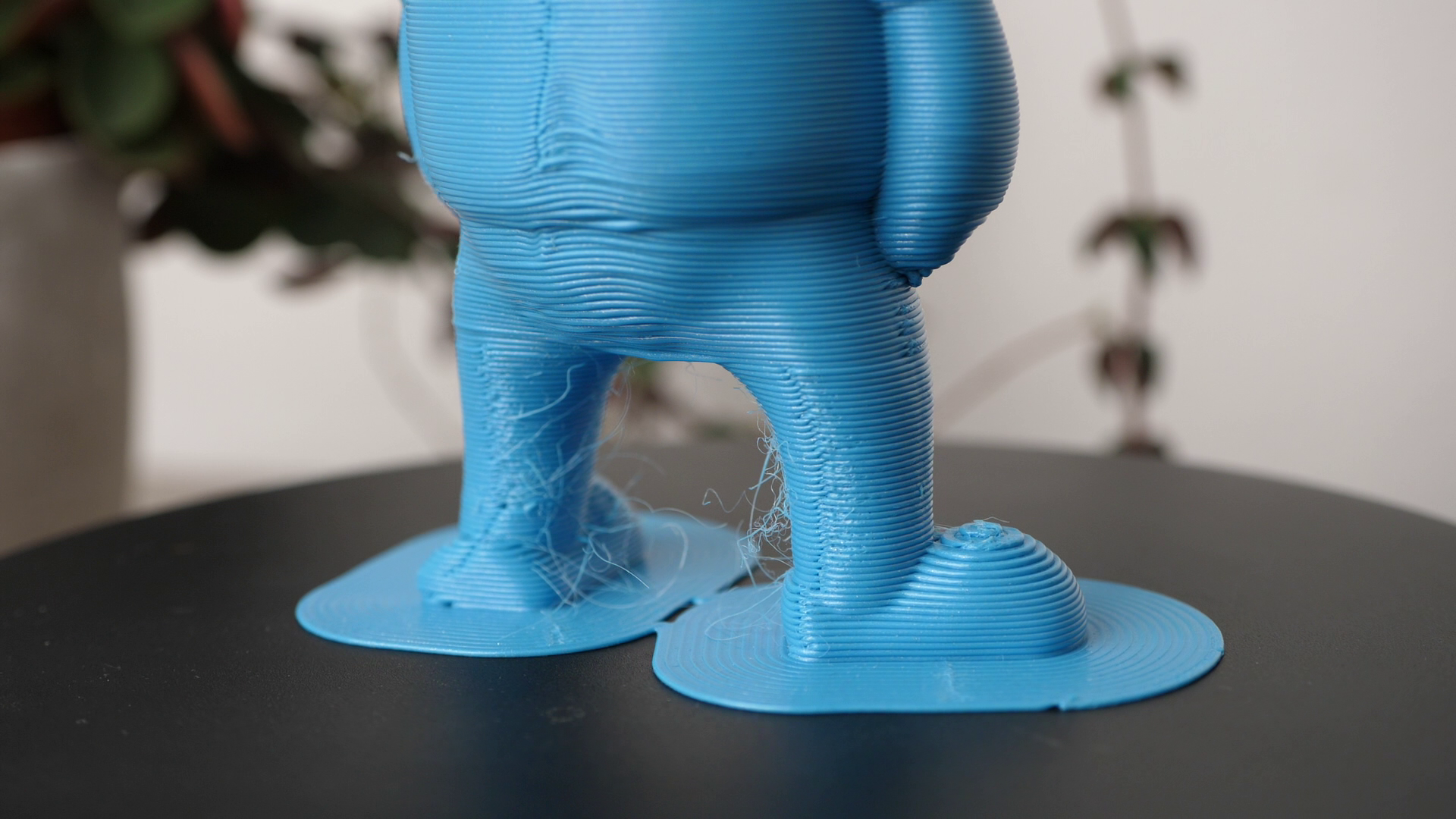


So will this become the new standard of how every 3D printer nozzle will look? I’m quite sure no. For once, there is additional effort and precision necessary during manufacturing and not everyone will need the additional performance. The more striking argument though is the patent behind this technology that Bondtech in this case licensed from 3DSolex. I linked the patent below if you’re interested which was granted in 2019. It covers various techniques that can be used to improve the melting rate of a nozzle by increasing surface area and heating the material from the center. I’m not a patent expert and I don’t know if there might even have been prior art on the RepRap forums. On the one hand, I think it’s a legitimate invention that ended up in an improved product so deserves some kind of protection and credit. On the other hand, I find it kind of sad, that this now blocks other companies for the next 20 years of implementing something similar in for example a wear-resistant high flow nozzle. Still, the inventor seems to at least be kind of open to licensing the technology. Another way is trying to work around patents that often sparks creativity in engineers. So maybe even you have an idea to improve on it!
Different insert shapes for improving the melt performance (from patent EP3445568A1)
In summary, I can only say that I’m hugely impressed by the performance of Bondtechs CHT nozzle, and the 30% increase in flow rate that they advertise is seriously the minimum I think you can expect. Even though they sent me the nozzles free of charge, I didn’t get paid, or were they able to review the video. The numbers and the print results objectively show that these nozzles are a serious improvement to what we all used in the past and renders, in my opinion, at least for the moment, many high flow hotends obsolete because you can get similar performance by just switching out a nozzle. Additionally, the decrease in length and lower mass are very interesting for high-speed printing. That said, not everyone currently has a need for this style of nozzle especially since they are currently only available starting from 0.6 mm upward. Bondtech, I hope you are listening but I reeeealy want a 0.4 mm variant for fast and detailed printing and I’m sure I’m not the only one! Since extrusion performance is also depending on your feeder, don’t expect the same results when changing the nozzle in a standard Ender-3. Still, for anyone, who’s looking for a simple solution to easily print faster and especially with bigger nozzles, these 20 bucks will be so well spent! Let me know down in the comments what you think about these new nozzles and if you ever used one, what your experience was.
📖 Further Links & References
CHT Nozzles from Bondtech (Affiliate in DE/UK): https://geni.us/U6M8s1K
Core Heating Patent: https://worldwide.espacenet.com/patent/search/family/058772617/publication/EP3445568A1?q=pn%3DEP3445568A1
Bondtech Whitepaper: https://www.bondtech.se/intranet/white-paper-max-flow-rate/